Manufacturing Through AI-Powered Predictive Maintenance
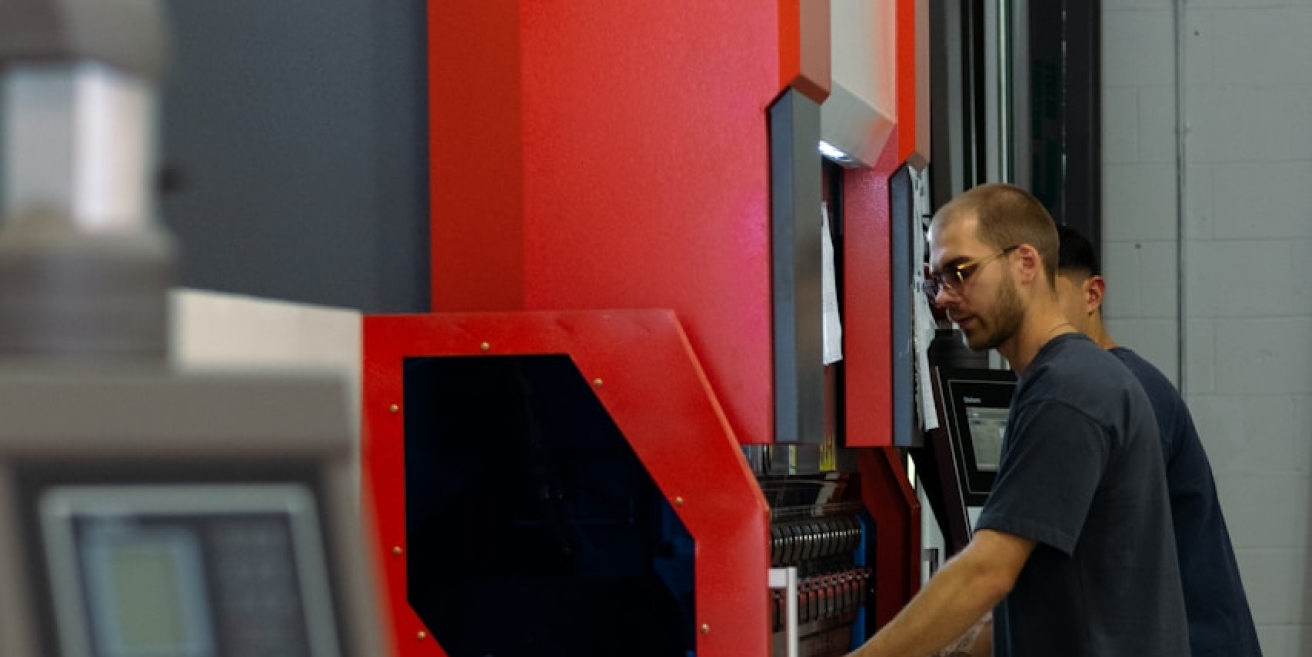
Executive Summary
SmartMFG has transformed traditional manufacturing maintenance through an innovative AI-driven predictive maintenance system. This case study examines how their solution has revolutionized equipment management, leading to enhanced operational efficiency and significant cost savings in manufacturing facilities.
Challenge
Modern manufacturing facilities faced several critical challenges:
- Unexpected machinery breakdowns causing production delays
- High costs of emergency repairs and replacement parts
- Production losses due to unplanned downtime
- Inefficient maintenance scheduling
- Limited visibility into equipment health
Solution Implementation
SmartMFG developed an advanced AI-powered predictive maintenance system that integrates multiple technologies:
Technical Specifications
- Real-time sensor monitoring
- Machine learning algorithms for failure prediction
- Automated maintenance scheduling
- Performance analytics dashboard
- Integration with existing machinery
Implementation Features
- Non-invasive sensor installation
- Real-time data collection and analysis
- Automated alert system
- Mobile application for maintenance teams
- Cloud-based monitoring platform
Results and Impact
Maintenance Improvements
- 75% reduction in unexpected breakdowns
- 60% decrease in emergency maintenance
- 85% accuracy in predicting equipment failures
- 50% reduction in maintenance-related downtime
Operational Efficiency
- 40% increase in equipment lifespan
- 55% reduction in maintenance costs
- 70% improvement in maintenance planning
- 45% decrease in spare parts inventory
Production Benefits
- 30% increase in machine availability
- 25% improvement in production quality
- 35% reduction in production delays
- 50% decrease in scrap rate
Financial Impact
- 40% reduction in maintenance budget
- 65% decrease in emergency repair costs
- 30% improvement in overall equipment effectiveness
- Significant ROI within first year of implementation
Key Success Factors
- Proactive Approach
- Continuous monitoring
- Early warning system
- Preventive intervention capabilities
- Data-Driven Decision Making
- Real-time analytics
- Historical performance analysis
- Predictive modeling
- Streamlined Implementation
- Minimal disruption to operations
- Quick deployment
- User-friendly interfaces
Real-World Application
As James Howard, Operations Manager at SmartMFG, states, "AI-driven predictive maintenance has transformed how we handle machinery, ensuring smooth operations." The system's success has been particularly evident in:
- Press brake operations
- CNC machinery
- Assembly lines
- Industrial equipment
Implementation Process
- Initial Assessment
- Equipment evaluation
- Sensor placement strategy
- Integration requirements
- System Deployment
- Sensor installation
- Software implementation
- Staff training
- Optimization
- Performance monitoring
- System fine-tuning
- Continuous improvement
Future Implications
SmartMFG's success demonstrates the transformative potential of AI in manufacturing:
- Expansion to different types of manufacturing equipment
- Integration with Industry 4.0 initiatives
- Development of more sophisticated prediction models
- Potential for industry-wide standardization
Conclusion
SmartMFG's AI-powered predictive maintenance system represents a significant advancement in manufacturing technology. The solution has demonstrated substantial improvements in equipment reliability, operational efficiency, and cost reduction while promoting sustainable manufacturing practices. As the technology continues to evolve, it positions itself as an essential tool for modern manufacturing operations.
Need a service?
Let's talk
You'll hear back in less than 24 hours